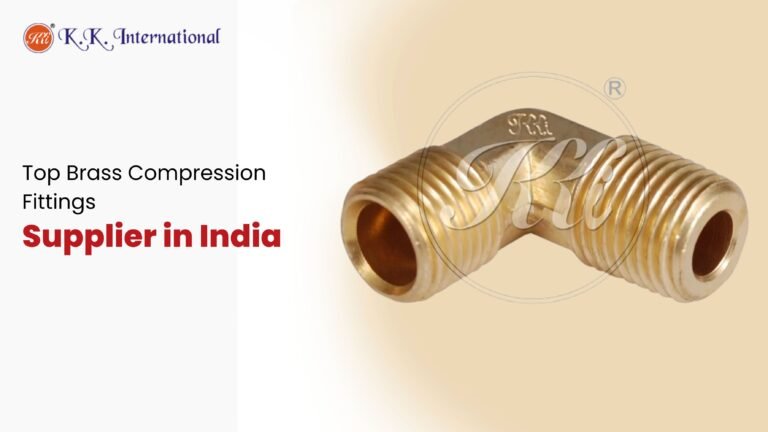
Top Brass Compression Fittings Supplier India
India’s industrial renaissance is quietly powered by components most people never see—brass compression fittings. These unassuming connectors are the unsung heroes of fluid and gas distribution systems, underpinning everything from sprawling automotive factories to advanced pharmaceutical labs. For entrepreneurs eager to grasp the nuts and bolts of modern manufacturing, understanding the brass compression fittings market is not just insightful—it’s essential. This article is your deep dive into the world of brass compression fittings in India, spotlighting why this market matters, who leads it, and what the future holds.
Introduction: The Vital Role of Brass Compression Fittings in Modern Industry
Picture a bustling factory floor: machines hum, pipes crisscross overhead, and fluids flow seamlessly from one process to the next. At every junction, brass compression fittings ensure that nothing leaks, nothing fails, and everything runs like clockwork. “Brass fittings are a cornerstone of fluid distribution systems, offering reliability, durability, and versatility for a wide range of industries,” notes a leading industry guide. In India, as manufacturing scales new heights and infrastructure projects multiply, the demand for these robust fittings is soaring.
The global compression fittings market, valued at USD 10.28 billion in 2024, is projected to reach USD 17.79 billion by 2032, growing at a CAGR of 7.1%. India’s share of this pie is expanding rapidly, driven by domestic manufacturing prowess and a relentless focus on quality.
Understanding Brass Compression Fittings: Types, Materials, and Key Features
Brass compression fittings are more than just connectors; they are engineered solutions designed to withstand high pressure, temperature extremes, and corrosive environments. Made from an alloy of copper and zinc, brass offers a unique blend of strength, machinability, and corrosion resistance. “Brass is an alloy primarily composed of copper and zinc, known for its excellent strength, corrosion resistance, and machinability. These properties make brass fittings ideal for fluid and gas applications in plumbing, HVAC, and industrial settings,” explains a recent industry report.
There are two main types of compression fittings: Type A (non-manipulative) and Type B (manipulative). Type A fittings are widely used for their ease of installation, while Type B fittings, requiring flaring of the pipe, are reserved for high-pressure or gas applications. Brass compression fittings can handle pressures up to 16 bar, making them a preferred choice for demanding industrial environments.
The Indian Brass Compression Fittings Market: Growth Drivers and Industry Landscape
India’s brass compression fittings industry is thriving, buoyed by robust demand from sectors like automotive, oil & gas, pharmaceuticals, and construction. The country’s manufacturing ecosystem is uniquely positioned to deliver high-quality products at competitive prices, thanks to a skilled workforce, advanced production facilities, and a culture of innovation.
A striking insight: India’s brass fittings manufacturers are increasingly adopting automation and lean manufacturing principles, driving down costs while enhancing precision and consistency. The result? Products that meet or exceed international standards, ready to compete on the global stage.
Why India is a Leading Hub for Brass Compression Fittings Manufacturing
India’s rise as a manufacturing powerhouse is no accident. The country boasts world-class foundries, precision engineering capabilities, and a deep pool of technical talent. “Brass fittings are manufactured by the leading producers in India with a focus on the supply of raw materials from reliable sources to offer long-lasting and durable products,” observes a prominent Indian manufacturer’s blog.
Moreover, India’s strategic location and trade agreements facilitate easy access to raw materials and export markets. This, combined with a strong emphasis on quality control and customer satisfaction, has cemented India’s reputation as a leading supplier of brass compression fittings.
Key Manufacturing Processes and Quality Control in Brass Compression Fittings Production
The journey from raw brass to finished fitting is a marvel of modern engineering. It begins with the selection of high-purity copper and zinc, melted and cast into billets. These billets are then hot-forged into the desired shape, a process that not only forms the fitting but also enhances its mechanical properties. Machining and surface treatment follow, ensuring tight tolerances and a flawless finish. “Hot forging is not only the process of giving the fittings preliminary shape but also increases their mechanical properties,” notes a manufacturing expert.
Quality control is paramount. Every batch undergoes rigorous testing for dimensional accuracy, pressure resistance, and leak prevention. Advanced inspection techniques, including non-destructive testing and automated gauging, ensure that only the best products reach customers.
Applications Across Industries: Where Brass Compression Fittings Make a Difference
Brass compression fittings are the backbone of countless industrial processes. Here’s a snapshot of their impact across key sectors:
- Automotive: Used in fuel, brake, and coolant systems, ensuring reliable performance under extreme conditions.
- Oil & Gas: Essential for connecting pipelines and valves, where leak prevention is critical.
- Pharmaceuticals: Employed in process equipment, where hygiene and reliability are non-negotiable.
- Construction: Integral to plumbing and HVAC systems, providing durable, leak-free connections.
- Manufacturing: Found in machinery and automation systems, enabling efficient fluid and gas transfer.
A recent industry analysis highlights: “Brass fittings play a crucial role in industrial piping systems due to their exceptional durability, corrosion resistance, and versatility. They provide reliable connections between pipes, valves, and other components, ensuring efficient fluid flow and system integrity.”
K K INTERNATIONAL: Excellence in Brass Compression Fittings Supply
Amidst a crowded field, K K INTERNATIONAL stands out as a beacon of quality and reliability. With decades of experience, the company has built a reputation for delivering precision-engineered brass compression fittings that meet the most stringent industry standards. K K INTERNATIONAL’s commitment to innovation, customer-centric solutions, and rigorous quality control has earned it a loyal clientele across diverse sectors.
The company’s success is rooted in its ability to customize products to meet specific customer needs, whether it’s a unique thread size, a special coating, or a bespoke design. “Our strength lies in our customers who have been with us for decades, and our cooperation with them has led to steady growth,” reflects the company’s ethos.
Competitive Advantages of K K INTERNATIONAL in the Indian Market
K K INTERNATIONAL’s edge is multifaceted. The company leverages state-of-the-art manufacturing facilities, a highly skilled workforce, and a relentless focus on quality. Its products are tested for pressure resistance, leak prevention, and material durability, ensuring compliance with international standards. By prioritizing customer satisfaction and continuous improvement, K K INTERNATIONAL has become a trusted partner for businesses across India and beyond.
Another key advantage is the company’s agility. In a market where lead times and customization are critical, K K INTERNATIONAL’s ability to respond quickly to customer requirements sets it apart from competitors.
Customization and Customer-Centric Solutions: Meeting Diverse Industrial Needs
In today’s fast-paced industrial environment, one size does not fit all. K K INTERNATIONAL understands this better than most. The company offers a wide range of brass compression fittings, from standard sizes to fully customized solutions. Whether you need a fitting for a high-pressure gas line or a specialized connector for a pharmaceutical application, K K INTERNATIONAL can deliver.
The company’s engineers work closely with clients to understand their unique challenges and develop tailored solutions. This collaborative approach ensures that every product meets the exacting demands of its intended application.
Navigating Challenges: Supply Chain, Quality Assurance, and Market Competition
The brass compression fittings market is not without its challenges. Supply chain disruptions, fluctuating raw material prices, and intense competition from global players can test even the most resilient manufacturers. K K INTERNATIONAL meets these challenges head-on by maintaining strong relationships with suppliers, investing in advanced quality control systems, and continuously innovating.
“Safety is of utmost importance in industrial settings, and brass fittings help ensure compliance with industry standards and regulations. These fittings undergo stringent quality control measures to meet performance requirements and are tested for pressure resistance, leakage prevention, and material durability,” notes an industry expert.
Innovations and Emerging Trends in Brass Compression Fittings
The brass compression fittings industry is evolving rapidly, driven by technological advancements and changing customer expectations. Here are some of the most exciting trends shaping the future:
- Sustainability: Manufacturers are increasingly using recycled brass and adopting energy-efficient production methods to reduce environmental impact.
- Enhanced Corrosion Resistance: New alloys and surface treatments are making brass fittings even more resistant to harsh environments.
- Smart Fittings: Integration of sensors and IoT technology is enabling real-time monitoring of pressure, temperature, and flow, revolutionizing maintenance and performance optimization.
- Compact Designs: As industrial spaces become more crowded, demand is growing for smaller, more versatile fittings that can be installed in tight spaces.
- Improved Threading and Connection Technology: Advances in design are making fittings easier to install and more reliable than ever.
“The brass fittings industry has undergone significant advancements in recent years, with innovations aimed at improving durability, performance, and sustainability,” observes a recent market analysis.
How to Choose the Right Brass Compression Fittings Supplier in India
Selecting the right supplier is critical for ensuring product quality, reliability, and long-term value. Here are key factors to consider:
- Experience and Reputation: Look for suppliers with a proven track record and positive customer feedback.
- Quality Certifications: Ensure the supplier adheres to international standards such as ISO, DIN, and ASTM.
- Customization Capabilities: Choose a supplier that can tailor products to your specific needs.
- Technical Support: Opt for a supplier that offers expert advice and after-sales support.
- Supply Chain Resilience: Assess the supplier’s ability to deliver consistently, even in challenging market conditions.
Conclusion: Partnering with K K INTERNATIONAL for Quality and Reliability
India’s brass compression fittings industry is at an inflection point, driven by innovation, quality, and a relentless focus on customer satisfaction. K K INTERNATIONAL exemplifies the best of this sector, combining technical expertise, manufacturing excellence, and a customer-first approach. For entrepreneurs and industrialists seeking reliable, high-performance solutions, partnering with K K INTERNATIONAL is a strategic choice that delivers long-term value.
As the industry evolves, one truth remains constant: “Brass fittings may be small, but their impact on safety, reliability, and industrial progress is enormous.” In a world where every connection counts, K K INTERNATIONAL is helping to build a stronger, smarter, and more sustainable future for Indian industry.